高純?yōu)R射鉻靶材是近年來新研制和開發(fā)的一種靶材,先后在集成電路、液晶顯示屏、真空鍍膜及電子控制器件等多個領域得到了廣泛的應用,市場規(guī)模不斷擴大。鉻靶材可以采用多種方法制備,而針對市場的大量需求,在進行鉻靶批量生產時,通常要求其純度能夠達到85%左右,因此,需要在選擇合理制備工藝的同時,有效控制高純?yōu)R射鉻靶材的生產成本。
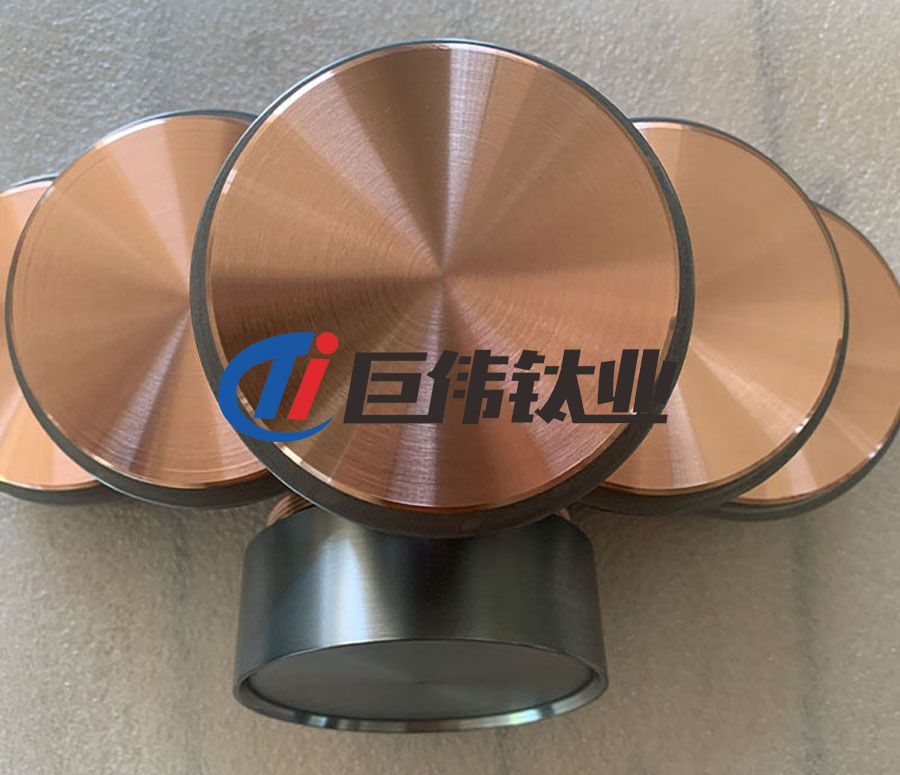
1、試驗原材料及試驗方法
1.1 試驗原材料的選擇
在試驗過程中,我們選擇電解鉻粉作為試驗原材料,其主要化學成分為Cr,其雜質元素含量為:
w(A1)=0.01%,w(Fe)-=0.02%,w(Pb)=0.01%,w(Si)=0.0015%,w(Cu)=0.002%,w(C)=0.004%,w(S)=0.001%,w(O)=0.3%。
1.2 試驗方法及試驗制備
常用的粉末冶金工藝包括傳統(tǒng)燒結、熱壓、真空熱壓和熱等靜壓等多種方法[1]。本試驗選擇傳統(tǒng)燒結法和熱壓法。
1.2.1成型及燒結試驗
傳統(tǒng)的燒結方法能夠用于大尺寸靶材的制備,但是致密度通常不高,在采用該方法制備靶材時,為了提高靶材的密度,通常需要增加燒結時間,或者在燒結之后進行軋制處理。這里首先將電解鉻粉與成型劑按一定比例放置于軋制模具中,然后利用300t的液壓機將鉻粉軋制成型或者包套,并進行等靜壓成型。模壓壓坯的標準尺寸為φ65mm x φ45mm x 46mm。將壓制成型的壓塊放人真空碳管爐中,在真
空條件下對其進行低溫燒結;如果進行高溫燒結,則需要在惰性氣體環(huán)境中進行,一般選擇氬氣,燒結溫度為1300℃和1450℃兩種,燒結時間均為7h。在燒結完成后,對比靶坯的尺寸、密度變化情況。
1.2.2熱壓試驗
熱壓法具有工藝簡單、致密度高的特點。在采用熱壓試驗進行靶材制備時,首先將混合后的鉻合金粉末放置到熱壓模具中,然后在惰性氣體(氬氣)環(huán)境下將其加熱到1300℃左右,之后進行1h左右的保溫,最后冷卻至600℃出爐。靶坯的標準尺寸為φ60mm x φ30mm。完成之后對靶坯的尺寸變化情況進行分析,并計算出靶坯的密度。熱壓法一般為單向加壓,因此,采用該方法制備的鉻靶材通常整體致密度不均勻,可見該方法只能適用于小尺寸靶材的制備。為了保證靶材的純度,通常在制備過程中不需要添加其他成型劑,而直接利用高純度的金屬粉末進行制備。
2、試驗結果分析
2.1 靶坯壓制過程
在進行靶坯軋制的過程中,由于各種摩擦因素的影響,壓力損失,導致靶坯各部分受壓不均勻,從而影響到靶材成型后的密度分布[引。通過采用雙向壓制的方法,能夠有效避免因壓力損失導致的靶材密度分布不均勻的問題。
2.2 加工方法對鉻靶材密度的影響
在進行鉻靶材制備的過程中,加工方法會直接影響到靶材的密度。目前,常用的鉻靶材加工方法主要包括熱等靜壓、真空熔煉、熱壓、冷等靜壓+燒結以及機壓+燒結的方法。表1給出了在不同加工方法下鉻靶材的密度數(shù)據(jù)。
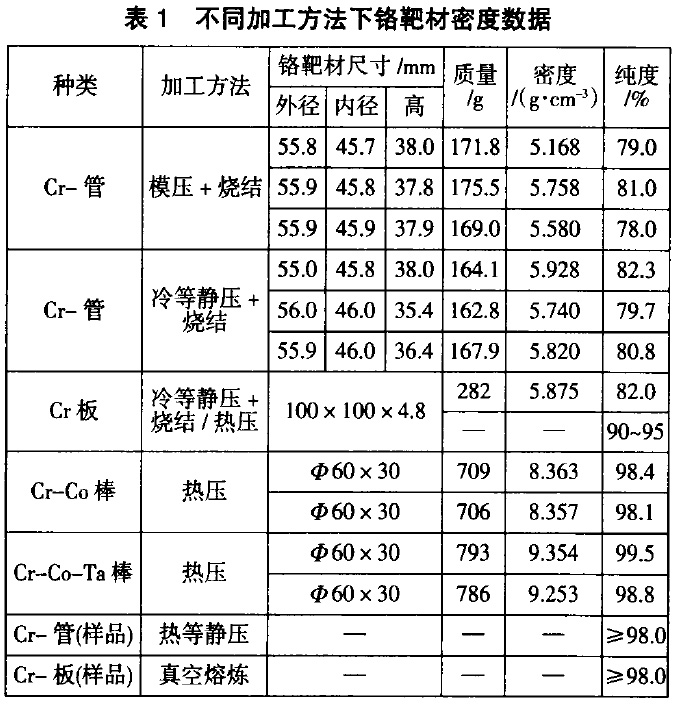
從表1中的數(shù)據(jù)可以看出,采用不同的加工方法,所制備的鉻靶材的密度差距比較明顯,其中采用熱等靜壓、真空熔煉以及熱壓三種方法,基本能夠保證鉻靶材的純度達到98%以上,但是這三種加工方法的成本相對較高,不適合應用到大規(guī)模生產中。在一般的鉻靶材批量生產中,通常要求純度達到80%~85%。針對這種要求,我們可以選擇“冷等靜壓+燒結”以及“機壓+燒結”的方法對鉻靶材進行加工,這樣既能滿足批量生產的密度要求,又能很好地控制制造成本。
2.3 燒結過程的控制
鉻粉燒結屬于單元系燒結,其燒結機制以擴散為主[引。當溫度在400℃以下時,應力恢復,吸附的水氣和水分會揮發(fā),壓塊的尺寸基本不會發(fā)生變化,而隨著溫度的不斷升高,靶坯中的成型劑逐漸分解并釋放出來,使爐內的真空度下降。當溫度升高至400~800℃之間時,進行1h的保溫,然后爐內開始出現(xiàn)再結晶,顆粒的內變形會逐漸恢復,從而形成新的結晶體,顆粒界面會隨著擴散逐漸發(fā)生黏結,
靶坯的強度逐漸增加。當真空度上升到10~2后,向爐內注入氬氣,避免鉻被氧化,然后繼續(xù)升溫至1100~1 200℃,并對溫度上升的速度進行控制,保持2h左右的時間,以保證粉末顆粒黏結的充分進行,提高靶坯的密度和強度。之后繼續(xù)加溫并控制升溫速度,使溫度在2h左右上升至1300~1450℃,之后進行0.5—1.5h的保溫。將靶坯的燒結時間降低到7h,不會影響靶坯的燒結密度,還能降低大約30%的成本。在燒結的過程中需要對加熱速度進行控制,避免因過快的加熱速度導致吸附氣體不能被徹底排除而影響到鉻環(huán)的收縮不均勻,造成變形,影響到鉻靶材的燒結密度。另外,過快的加熱速度還可能導致壓制過程中的高內應力,使鉻靶材出現(xiàn)裂紋。
因此,在高溫燒結階段,對升溫速度和最高溫度的控制尤為重要。
2.4 保護氣體對鉻靶材燒結密度的影響
在進行鉻靶材的燒結時,在通常情況下,需要將燒結溫度提高到1250~1450℃之間時,才能形成純鉻粉靶環(huán)的燒結。此時,其他因素對靶材燒結的影響較低。經過實踐發(fā)現(xiàn),當燒結溫度在1250~1 450℃之間時,如果沒有惰性氣體進行燒結保護,就可能會發(fā)生一定的氧化現(xiàn)象,而且鉻的蒸發(fā)量也較大。為了避免這種情況,在進行高溫燒結時,必須向爐內加入惰性氣體進行保護,適當控制爐內壓力。同時,真空度對靶坯的燒結密度會產生一定程度的影響。
3、結論
1)不同的加工方式所制備的靶材密度存在較大差異,通常情況下,在進行批量鉻靶材生產時,要求靶材純度達到80%~85%,此時可以采用“模壓+燒結”或者“冷等靜壓+燒結”的方式進行加工;而鉻合金靶材的純度要求一般需要在98%以上,此時可以選擇真空熔煉、熱壓及熱等靜壓的方式進行加工。
2)在進行靶坯的壓制過程中,只需要采用雙向壓制方法,不需要向鉻粉中添加任何成型劑,即能很好保證靶坯的密度。
3)通過對燒結的時間、溫度的變化進行合理的控制,能夠在保證燒結密度的情況下,大幅度降低燒結成本。
參考文獻
[1]羅俊峰.粉末冶金靶材的制備與應用[J].中國金屬通報,2011(31):40—41.
[2]張冷,張維佳,宋登元,等.銅銦鎵硒薄膜的真空制備工藝及靶材研究現(xiàn)狀[J]助能材料,2013,44(14):1 990—1 994.
[3]儲志強.國內外磁控濺射靶材的現(xiàn)狀及發(fā)展趨勢[J].金屬材料與冶金工程,2011(4):44-49.
相關鏈接